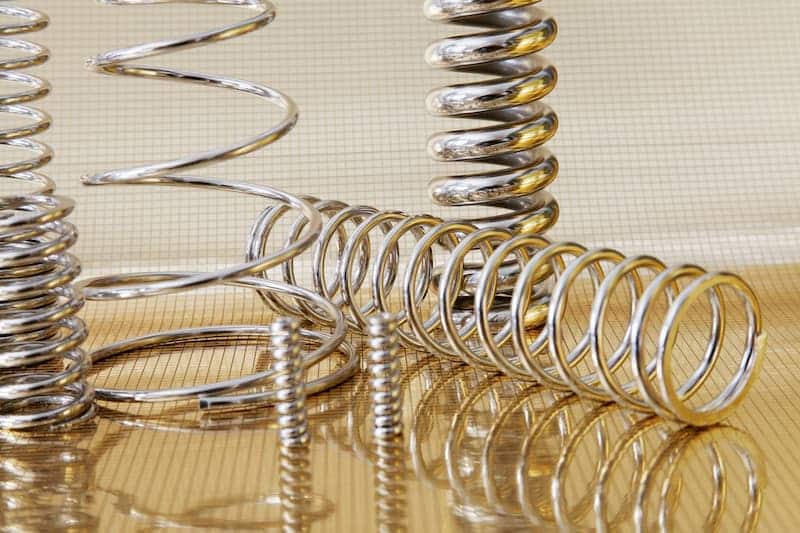
Spring Manufacturing Process
Mechanical springs are present in every area of our lives, and it is easy to take these practical components for
Home › Engineering › Page 6
Mechanical springs are present in every area of our lives, and it is easy to take these practical components for
Industry 4.0, also known as the fourth industrial revolution, represents a remarkable technological shift in the way manufacturing companies operate.
The term spring creates, for most people, the image of a classic helical compression spring, but this is not always
The manufacturing industry is constantly growing and changing to create the broad range of complex components our modern lives require.
Metal stamping has been an integral part of the design and construction of an immense amount of products and applications.
At European Springs, we manufacture a wide range of springs for many different industries and bespoke pressings and wire forms,
It’s no secret that the world is not the same place as it was two years ago. The effects of
To commemorate National Apprenticeship Week, we wanted to give some inspiration for those lucky enough to teach STEM subjects such
Nearly half of manufacturing businesses have been the victims of cyber-crime at some point. Since the pandemic, more and more
And even if we don’t have exactly the tool we need, European Springs’ in house technology enables us rapidly to design and make complex tools, allowing us to offer more competitive prices.
© Copyright 2025 | European Springs
Designed, Promoted and Powered by SQ Digital