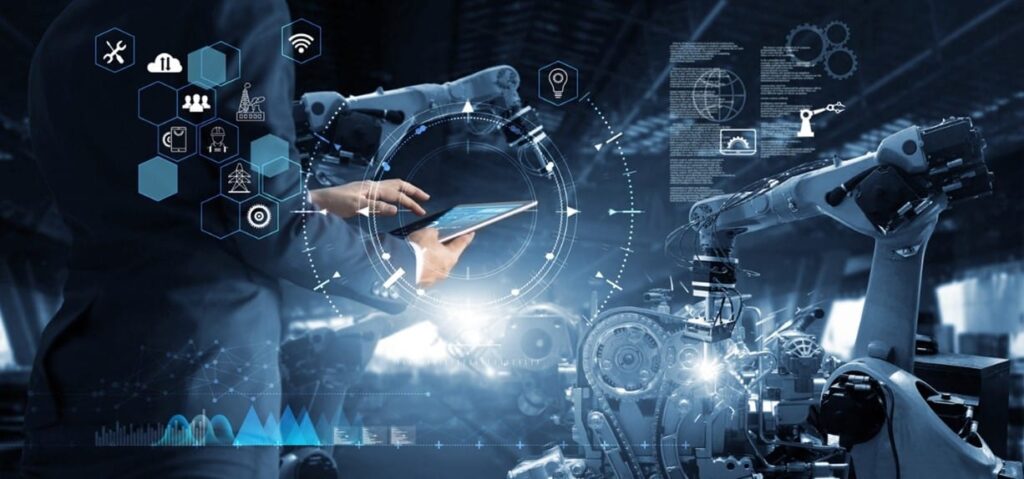
Why Manufacturers Are Being Urged to Increase Use of Digital Technology
With digital technology revolutionising various sectors, manufacturers are urged to embrace digital transformation to remain competitive and relevant in this
Home › Engineering › Page 5
With digital technology revolutionising various sectors, manufacturers are urged to embrace digital transformation to remain competitive and relevant in this
Here at European Springs, we are proud to share our commitment to sustainable solutions and are dedicated to reducing our
Here at European Springs, we’re lucky enough to work closely with businesses from an extensive range of industries, including the
If you’re considering a career in engineering, knowing the best route for getting qualified can be difficult. Whether you want
There are many factors to consider when choosing spring material and finish, and our expert spring manufacturers are equipped with
Here at European Springs, we have been manufacturing springs for over seven decades, so we have seen the industry shape-shift
As leading spring manufacturers in the ever-evolving engineering industry, we are always looking for ways to improve our processes to
The manufacturing industry is a vast sector with a range of paths to explore. Therefore, when you enter the field,
Here at European Springs, we have over seven decades of experience designing, manufacturing, and implementing our springs in various sectors.
And even if we don’t have exactly the tool we need, European Springs’ in house technology enables us rapidly to design and make complex tools, allowing us to offer more competitive prices.
© Copyright 2025 | European Springs
Designed, Promoted and Powered by SQ Digital