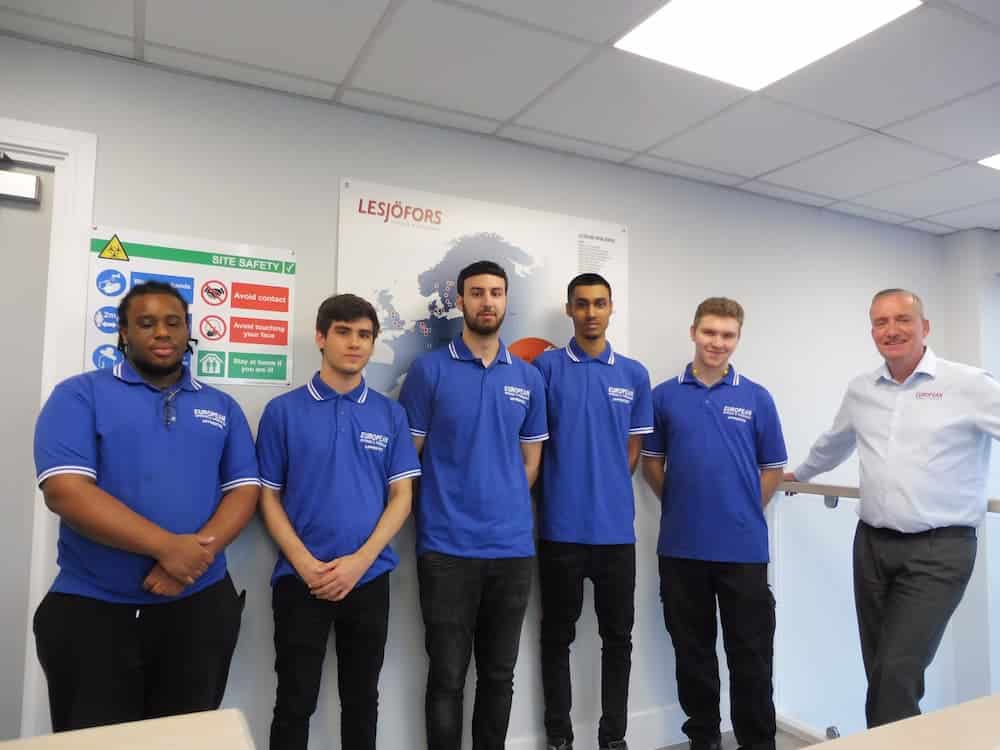
Securing the Future of Manufacturing
We are delighted to announce that we have recently on-boarded five new apprentices, Ronique Neil, Leonardo Hogan, Sami Hamanche, Racim
Home › News & Updates › Page 6
We are delighted to announce that we have recently on-boarded five new apprentices, Ronique Neil, Leonardo Hogan, Sami Hamanche, Racim
Exhibitions and trade shows are essential tools for establishing and maintaining connections and relationships between businesses. At European Springs, we
UK manufacturing is still feeling the impact of the last two years’ events. Production and economic disruptions created many challenges
It’s widely known that the manufacturing industry was one of the most significant contributors to harmful greenhouse gases, but this
The UK manufacturing industry plays an essential role in supporting the economy. With over 270 thousand businesses in the UK
The manufacturing sector has seen its share of changes over the last few years, but during this time, it has
Manufacturing is a highly professional industry that requires its workers to earn particular qualifications, leading to the current skills gap
At European Springs, we’re proud of our long-term commitment to support the manufacturing industry with our apprenticeship schemes. We firmly
The demands on spring manufacturers are at their highest when manufacturing suspension springs for vehicles. The automotive industry relies heavily
And even if we don’t have exactly the tool we need, European Springs’ in house technology enables us rapidly to design and make complex tools, allowing us to offer more competitive prices.
© Copyright 2025 | European Springs
Designed, Promoted and Powered by SQ Digital