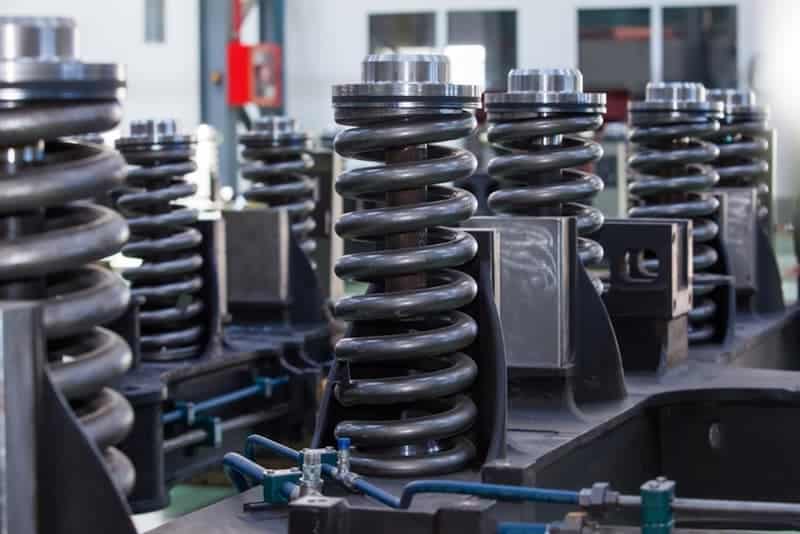
Spring Designs That Get You Through the Day
At European Springs, we take great pride in our expertise in designing and manufacturing various spring and pressing products for
At European Springs, we take great pride in our expertise in designing and manufacturing various spring and pressing products for
Reducing the environmental damage of various industries in the UK is a challenge that manufacturing is rising to. The main
Here at European Springs, we have over seven decades of experience designing, manufacturing, and implementing our springs in various sectors.
Mechanical springs are present in every area of our lives, and it is easy to take these practical components for
Industry 4.0, also known as the fourth industrial revolution, represents a remarkable technological shift in the way manufacturing companies operate.
The manufacturing industry is an industry of growth and innovation that has adapted to many unforeseen events. For example, the
The manufacturing industry is taking many different approaches toward becoming more eco-friendly. The impressive shift to increased sustainability is inspired
Manufacturing is a constantly changing industry. Adapting to changes in customer demand, product requirements, and production economics across the supply
With the positive progression of the UK’s plans to achieve Net Zero emissions by 2050, the manufacturing industry made extensive
And even if we don’t have exactly the tool we need, European Springs’ in house technology enables us rapidly to design and make complex tools, allowing us to offer more competitive prices.
© Copyright 2025 | European Springs
Designed, Promoted and Powered by SQ Digital