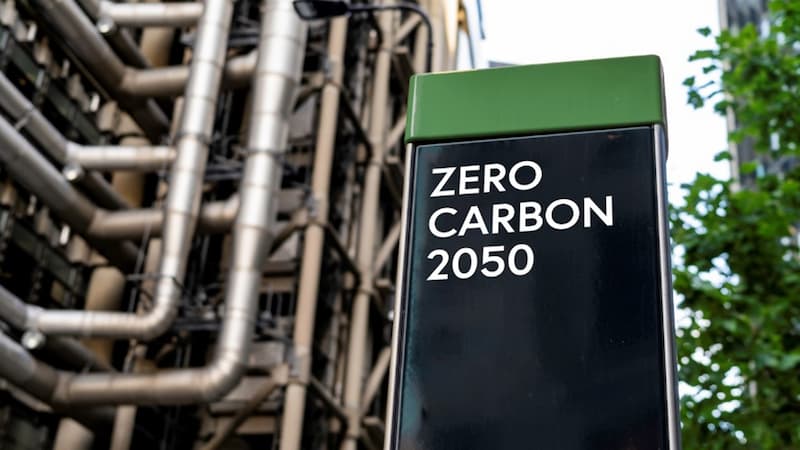
How to Work Sustainably & Grow Your Manufacturing Business
In 2024, sustainability is more than just a moral choice for UK manufacturers—it’s also a business strategy that can drive
Home › Engineering › Page 2
In 2024, sustainability is more than just a moral choice for UK manufacturers—it’s also a business strategy that can drive
Engineering apprenticeships are excellent investments for both the student and the employer and provide many benefits to the UK manufacturing
Initially developed in the 1940s for jet engines, superalloys have come a long way since then, emerging as highly versatile
You know that springs are our speciality. But how much do you know about springs? While many people can tell
Like many other industries, engineering and manufacturing are seeing an incredible acceleration in their processes thanks to the ever-growing presence
Springs are integral to a wide range of applications across an equally large number of industries, from automotive to power
Springs are invaluable components that, with their many designs, materials, and applications, significantly contribute to an incredibly varied number of
Springs are key components found in an enormous amount of machinery, vehicles, and countless other complex systems across various industries,
The power industry’s non-negotiable foundations are extreme precision, reliability, and efficiency. These combined guarantee stable power generation and distribution consistently,
And even if we don’t have exactly the tool we need, European Springs’ in house technology enables us rapidly to design and make complex tools, allowing us to offer more competitive prices.
© Copyright 2025 | European Springs
Designed, Promoted and Powered by SQ Digital