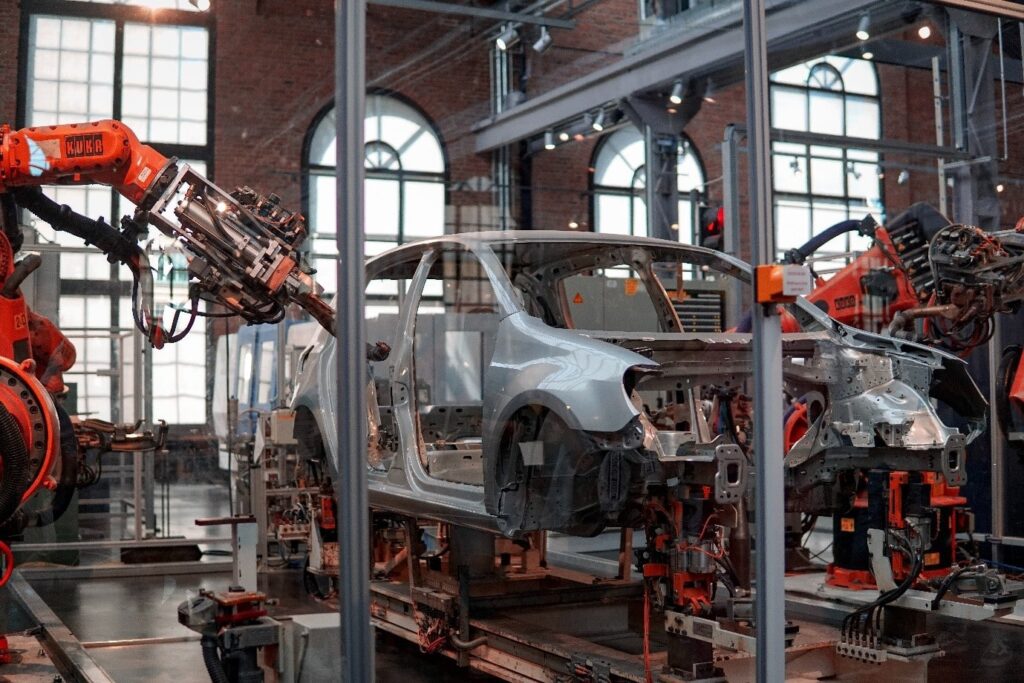
How Innovation Has Helped Businesses Get Back To Work
As a large proportion of the nation’s workforce heads back to their workplace, there are some businesses that have managed
Home › Engineering › Page 10
As a large proportion of the nation’s workforce heads back to their workplace, there are some businesses that have managed
It’s fair to say the last few months have brought up some negative stories around the industry due to the
With many businesses in the manufacturing and engineering sector heading back to work in recent weeks, there has been some
There is no doubting the fact that manufacturing will become increasingly reliant on AI technology in the coming years. To
With the UK officially leaving the European Union on 31st January 2020, many manufacturing businesses are looking for ways to
In recent years, it’s fair to say that most industries across the UK have experienced some form of a downturn
With AI, robotics and automation commonly viewed as at the cutting-edge of inspirational industry, it may come as a surprise
Over the years the UK Manufacturing Industry has fallen behind its global counterparts with regards to productivity within the workplace.
It’s fair to say that the automotive industry has been through a period of profound change in recent years –
And even if we don’t have exactly the tool we need, European Springs’ in house technology enables us rapidly to design and make complex tools, allowing us to offer more competitive prices.
© Copyright 2025 | European Springs
Designed, Promoted and Powered by SQ Digital